The Advantages of the New XT9® Glue-less Lamination Process – Part 2
By Randy Metcalf
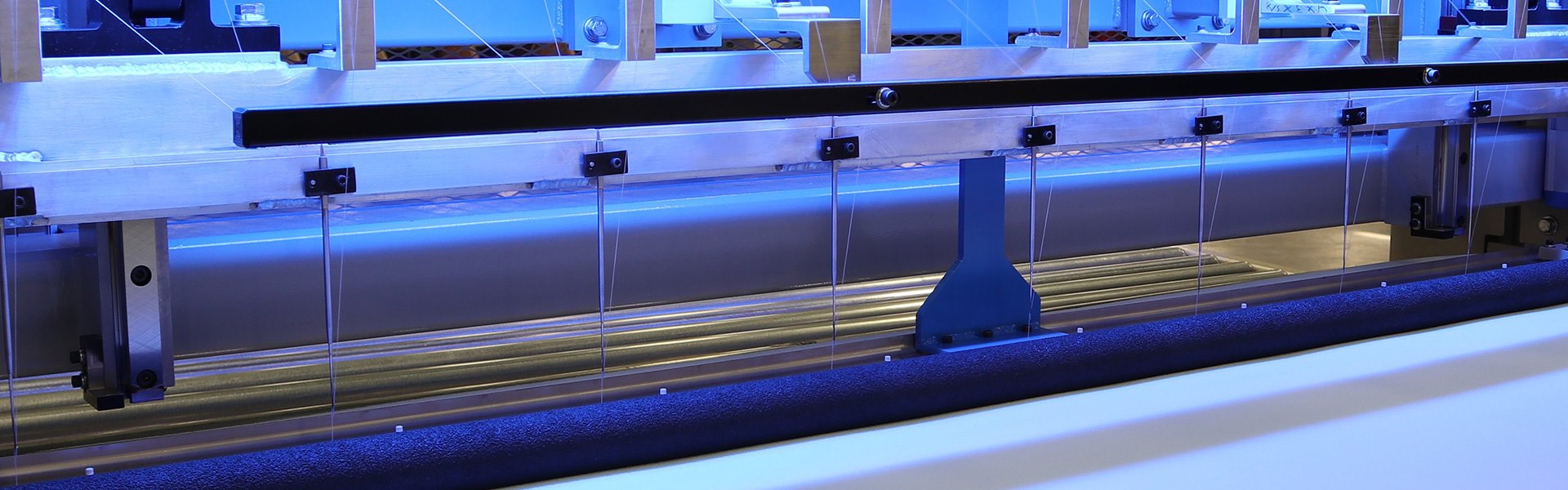
In Part 1 of this series, the cost-effective production efficiencies of replacing the old-school glue lamination systems with the new, highly efficient XT9 thread-based lamination method was shown to be very appealing to mattress producers. In this article, you’ll see how other intangible benefits may be appealing to both the manufacturer and mattress buyers as well.
Resource management is a win-win for the manufacturer and consumers
The XT9 can complete the same process as most glue lamination with fewer machines and faster cycle times. That means equal or greater production output can be achieved with less effort. Achieving a responsible gain in productivity with improved resource management practices is attractive to both manufacturers and a growing customer base of environmentally conscious mattress shoppers.
The thread used in the XT9 system is a stable commodity with an indefinite shelf-life. Adhesives, on the other hand, have a shelf-life that is typically six months or less if stored in ideal conditions. The concern of expiring adhesive materials complicates inventory management issues. A manufacturer can’t leverage purchasing power by stocking up on large quantities of glue for fear that it may go to waste if it’s not used in a timely manner, whereas thread can be bought in bulk without concern for wasting materials.
Wasted glue is not just a cost-control concern for responsible manufacturers. Unconsumed glue inventories are a waste of fuel energy used to deliver that glue quantity to the mattress factory and a waste of the resources consumed during the production process that initially made that glue.
One more resource management concern is water. Nearly every water-based adhesive lamination system requires extra daily cleaning procedures not required of the thread-based XT9 method. It involves more non-value-add labor costs and the additional consumption of water resources. That water supply adds to the daily cost of the glue-based lamination process and consumes additional resources in the process.
Recycling is a growing concern for mattress producers, buyers, and governments. Most want to keep beds out of landfills and an increasing number of governing bodies are moving to make this a legal mandate. Foam mattress materials that are glued together have few options at a recycling center but to be ground up by industrial shredders to be repurposed in other products. The XT9 thread-based lamination process gives recyclers the option of easily separating the laminated foam materials instead of shredding the composite layers. These intact sheets may be of more value to downstream users who wish to recycle specific foam materials for explicit purposes.
Go with the Flow
Breathe fresh life into your bedding products.
Mattress consumers are seeking healthy alternatives when shopping for a new mattress. They want to eliminate unnecessary chemical products, embrace more natural healthy components, and benefit from a comfortable sleep experience. The stitched layers of an XT9 bed contribute to all these objectives.
Adhesive laminating forms a barrier of hardened glue between each foam sheet that restricts healthy air flow and it can trap heat. Moisture and microbes sealed in this setting, while engulfed in stagnant air, can lead to unhealthy conditions.
It’s well understood that fresh air circulation is an effective deterrent against bacterial growth. The lanes of stitching used to secure foam layers on the XT9 Stitch Bridge create open channels of air travel throughout the mattress for healthy air flow to all corners of the bed.
Testing of forced vertical airflow through the layers of foam vary from one combination of materials to another, but the horizontal air flow, can travel between each layer of the XT9 formed bed at significantly greater rates than through glued layers.
Obviously, real world use would involve low circulating ambient air flow, or, at best, air moving from a nearby house fan. It should be noted, air is a gas which fills every available space. As a person moves in the bed, the changing pressure points on the XT9 combined foam layers open and close and re-open, repeatedly creating voids for air to enter and transmit when other body movements create other spaces. It is almost as if the XT9 laminated foam layers are a lung drawing in air and expiring air throughout the night.
Bed designers go to great lengths to create a particular formula of comfort layer combinations, but bonding those layers with multiple coatings of glue make them more ridged and less responsive to the sleeper’s body. The “free float” nature of the XT9-formed layers provides a less-restricted interplay between the sleeper and the comfort layers. This results in a purer level of comfort as intended by the designer.
The XT9 system is a valuable marketing story
In a marketplace full of commodity beds, the XT9 marketing story would be a welcomed addition to a mattress showroom. The XT9 glue-less lamination method has unique new technology, supports healthy lifestyles, and contributes to a more environmentally sustainable mattress market. That’s a lot of enticing sales material to differentiate your mattress product from traditionally manufactured beds competing against you. Mattress manufacturers can capitalize on greater margins with the XT9 product that heightens value in the eye of the customer while simultaneously reducing his own production costs.
Visit the Gribetz XT9 web page to see more about this new glue-less lamination process.