NON-UTILIZED TALENT is a costly waste of your most valuable assets
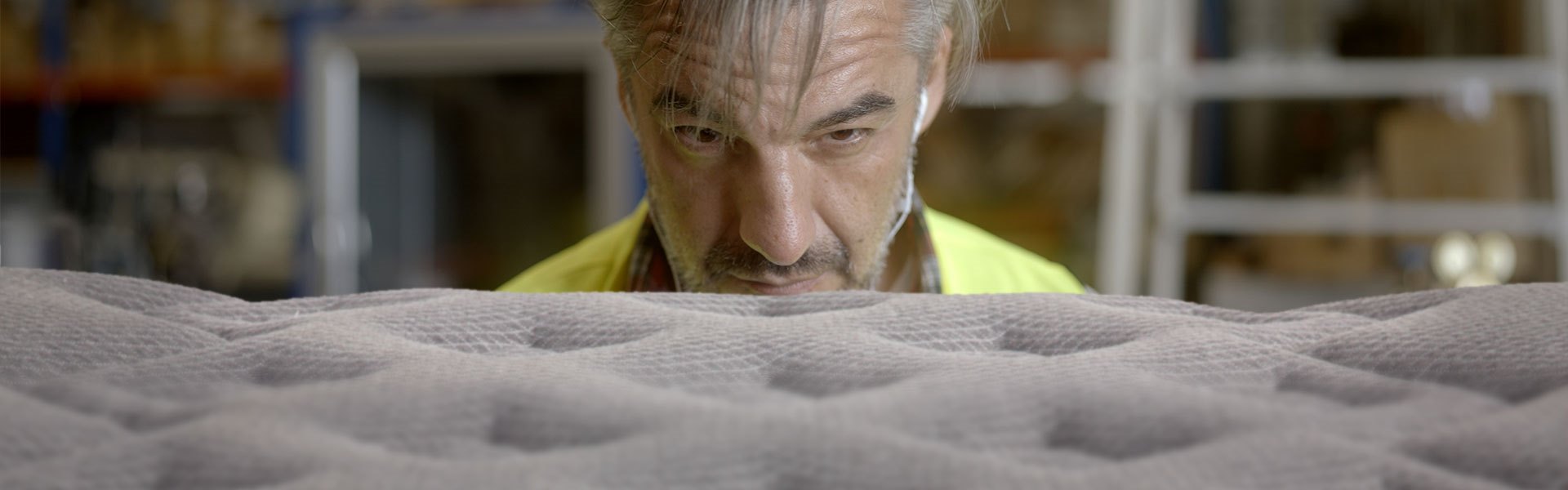
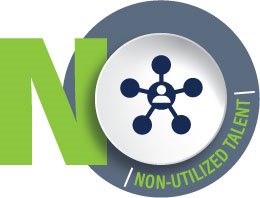
NON-UTILIZED TALENT – This waste occurs when skilled employees are not performing valuable tasks, or their knowledge and talents are not being shared to improve performance of the full workforce.
If an employee excels at a task others struggle with there may be a flaw in the system that worker has learned to overcome. Explore the process with that employee and it may reveal an action or step that can be improved with better equipment. Once that is corrected, this high-yield employee may be utilized in other areas in need of their skills.
- Causes: Skilled, experienced employees get pigeon-holed in work where they have proven to be successful, but their effectiveness is not shared with others.
- Solutions: Reduce the knowledge and skills gap throughout your workforce with de-skilled methods for more balanced productivity rates. Leverage experienced staff to identify and correct flawed processes.
GSG Solutions
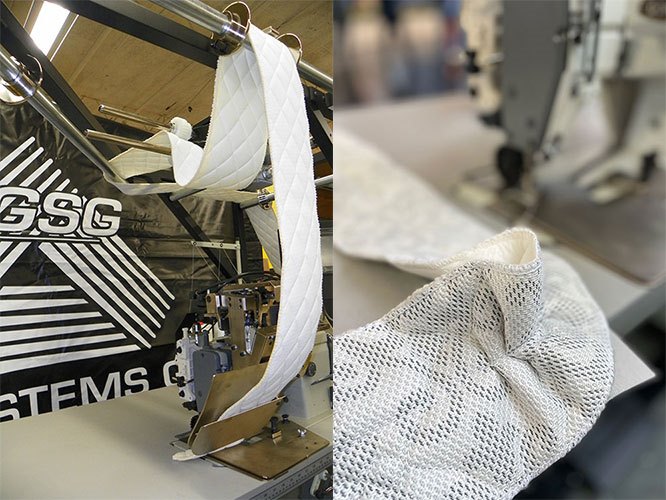
The GPT-1100AP ruffling machine is a great equalizer of talent in the mattress factory. It replaces the skills-dependent process of making mitered corners, or the alternative “Tuck and Run” style, with a semi-automated pleated ruffle.
- Multi-tasking machine enables low-skilled employees to make pillowtop gussets, Eurotops, and foundation covers.
- Highly skilled operators can be devoted to other higher value work.
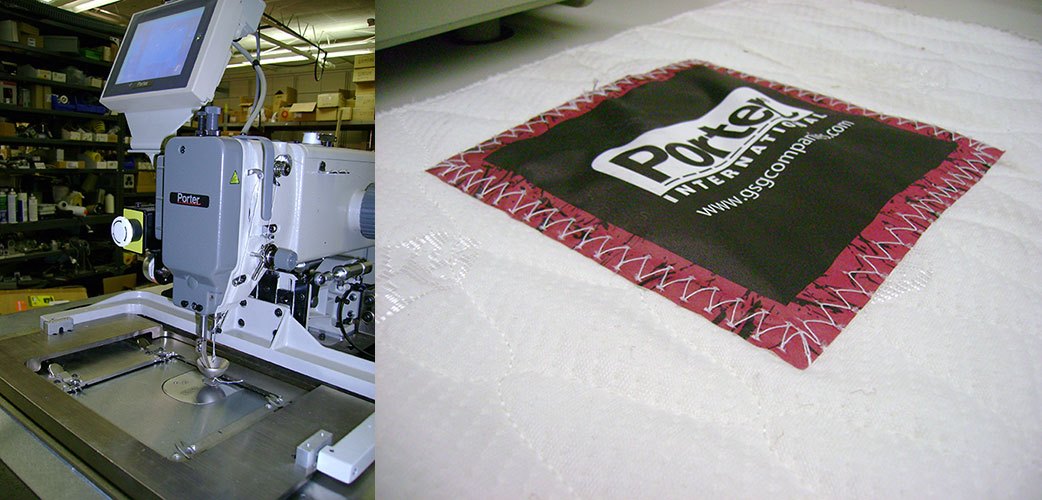
PALS-2000 automated label sewer - The automated label sewing system frees up talented sewing staff to perform other work. The automated label sewer can produce up to 500 units per 8-hour shift. That fast cycle time would be hard to match by manual methods.
- Automated stitching process ensures consistent quality
- De-skilled process makes any employee successful in this production step.

DOWNTIME is a common acronym for eight costly types of waste identified in lean manufacturing methodologies. Some forms of waste are obvious, and easily remedied, but others persist and compound their damage daily.
Defects | Over-Processing | Waiting | Non-Utilized Talent
Transportation | Inventory | Motion | Excess Processing
Read our previous article to learn how damaging WAITING waste can be and all other forms of DOWNTIME waste will be examined in upcoming posts.
There are many more examples of GSG equipment that reduce DEFECTS waste in your factory, so connect with your experienced GSG representative to learn about more.
Non-value-add TRANSPORTATION waste gets you nowhere! Learn how to reduce unnecessary movements of goods within your process in our next article.
If you would like to have a FREE DOWNTIME poster from GSG to post in your facilities, please make your request here.
DOWNTIME Series
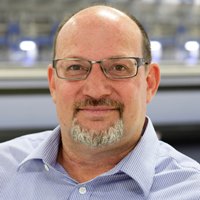