Eight GSG solutions for DOWNTIME waste
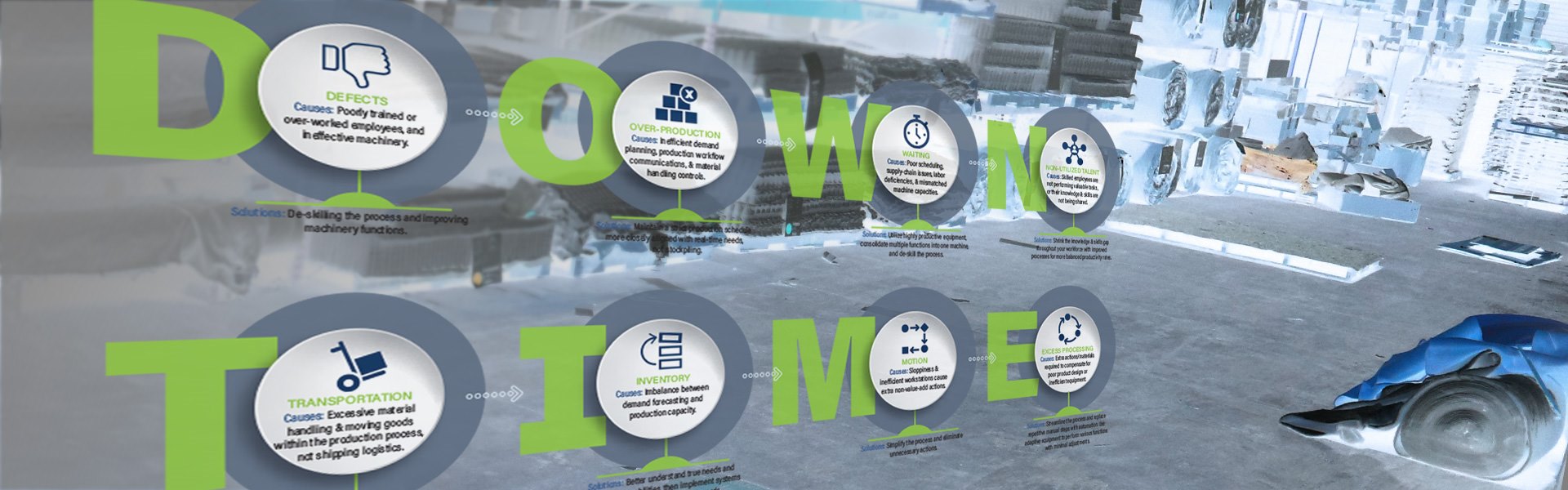
DOWNTIME is a common acronym for eight costly types of waste identified in lean manufacturing methodologies. Some forms of waste are obvious, and easily remedied, but others persist and compound their damage daily.
Defects | Over-Processing | Waiting | Non-Utilized Talent
Transportation | Inventory | Motion | Excess Processing
Every action, every consumable resource, every piece of material involved in the production process either adds value to the finished product or it deducts value. In other words, it either earns you money or it costs you money. It’s hard enough to earn manufacturing profits even if you had 100% utilization of labor and materials, so why tolerate any avoidable waste that will only hurt your bottom line?
Correcting wasteful routines in every form should always be a consistent practice for profitable manufacturing operations, but given today’s especially challenging business climate, it is inexcusable to ignore the sources of these profit-robbing wasteful problems.
We’ll address how each of these forms of waste apply specifically to mattress producers. DEFECTS waste is explained below and each other form of DOWNTIME waste will be examined in upcoming posts.
DEFECTS waste – Defective, poor-quality products are costly because either the finished product will have to be scrapped or you’ll have to spend more in additional labor and resources to correct the unsatisfactory unit. Worst of all, if defective products reach the marketplace it can result in expensive litigation, costly product returns, damage your company’s reputation, and hurt future sales.
- Causes: Poorly trained or over-worked employees, and ineffective machinery are the primary reasons for defective products.
- Solutions: De-skilling the process and improving machinery functions.
GSG solution

EST-501 deskills the job and produces more consistent quality. Quilt panels are one of the most valuable parts of a mattress – don’t waste materials or time here. The ergonomic design of this semi-automatic flanging machine helps improve the consistency of product quality regardless of the skill level of your operator. The automated turning belts are sync’d with the strong sewing head to do the work of controlling speeds and rotating heavy panels as your worker moves through the flanging process.
Equistitch and Pattern Compensation features on the Paragon M+ quilter ensure consistent stitch integrity during the quilting process regardless of speeds and pattern designs. Naturally manufacturers want to maximize production by pushing their machines as fast as possible for greater productivity. Unfortunately, depending on the density of quilt packages and varying complexities of the pattern design, some high-speed quilting may result in stitch length irregularities and pattern distortion.
GSG quilters has built-in advanced technology to adjust sewing performance based on these factors. If your customer has ordered mattresses with a 2-inch Circle pattern, they expect a Circle, not a stretched-out Oval shape. Quality beds maintain appropriate stitch lengths and stitch densities, and this GSG system enables you to meet those demands regardless of production speeds and various material choices.
There are many more examples of GSG equipment that reduce DEFECTS waste in your factory, so connect with your experienced GSG representative to learn about more.
Did you know it is possible to have too much of a “good” thing? We’ll discussed how stocking up on too much finished product can produce costly OVER-PROCESSING waste in our next article.
If you would like to have a FREE DOWNTIME poster from GSG to post in your facilities, please make your request here.
DOWNTIME Series
- Over-Production Don’t get overwhelmed with OVER-PRODUCTION waste
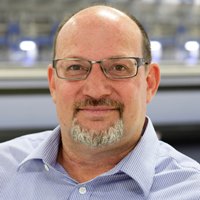