Don’t let WAITING waste stall profits in your manufacturing facilities
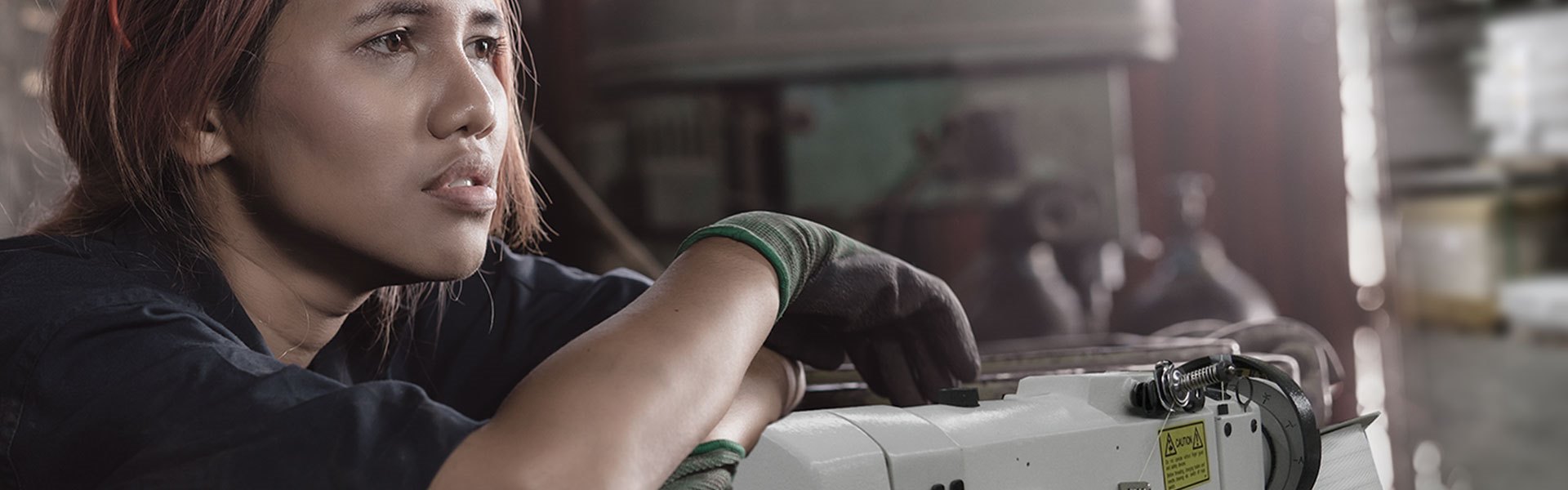
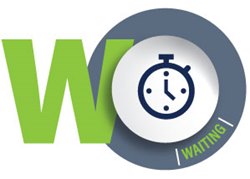
WAITING waste is abnormal idle time occurring during the production process. This is costly because it results in a drop in worker productivity and irregularities in your workflow that can disrupt schedules and delay orders.
Manufacturing systems are most effective when they maintain a consistent rhythm and workflow. Unanticipated waiting time hurts the value immediate process and downstream operations too.
- Causes: Poor planning, supply chain management problems, and poor utilization of talent are common causes. But a mismatch in machine production capabilities can also lead to WAITING waste when a machine can’t produce fast enough to satisfy the rate of the downstream operations.
- Solutions: Utilize highly productive equipment, streamline the process by consolidating multiple functions in one machine, and de-skill the process to reduce the impact of slow workers.
GSG Solutions
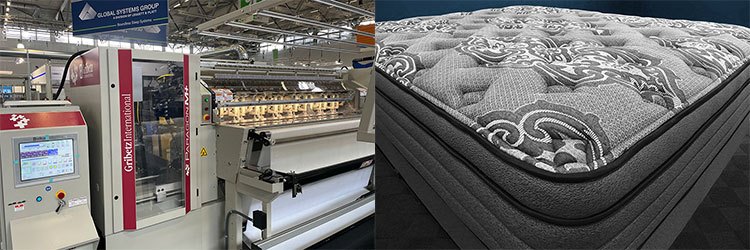
Paragon M+ mattress quilt machine keeps the workflow moving at high rate of productivity with minimal labor effort. The Paragon M+ can sew a full range of goods at top speeds of the industry so there is no waiting regardless of the material choices. Advanced features like the automatic thread tail trimming of the Posi-trim™ system and optional BatchMode/AutoSchedule® software maximizes panel production rates with little input from workers.
- High-speed production means more goods per hour
- High quality finished goods mean no waiting on QC repairs
- Automated processes and user-friendly features increase labor productivity
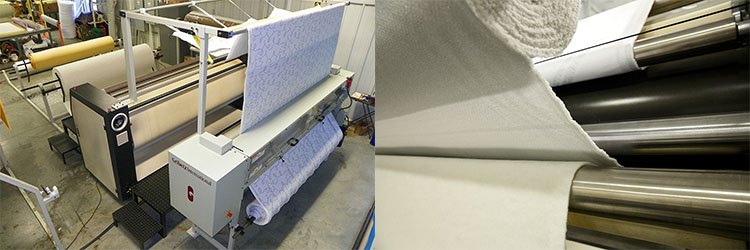
The Strata Lamination machine is designed to cost-effectively create all your laminated border needs. The ability to slit full-size rolls of materials into multiple rolls of variously sized laminated border produces far greater daily yield than any single lane laminating machine.
- It uses a heat-sensitive dry adhesive material
- Less required clean-up time than liquid adhesive systems
- Bonds and dries almost instantly to reduce waiting times

DOWNTIME is a common acronym for eight costly types of waste identified in lean manufacturing methodologies. Some forms of waste are obvious, and easily remedied, but others persist and compound their damage daily.
Defects | Over-Processing | Waiting | Non-Utilized Talent
Transportation | Inventory | Motion | Excess Processing
Read our previous article to learn how damaging DEFECTS waste can be and all other forms of DOWNTIME waste will be examined in upcoming posts.
There are many more examples of GSG equipment that reduce DEFECTS waste in your factory, so connect with your experienced GSG representative to learn about more.
NON-UTILIZED TALENT is a costly waste of your most valuable assets! Learn how to close the skills gap to create more balanced productivity rates for your whole operation in our next article.
If you would like to have a FREE DOWNTIME poster from GSG to post in your facilities, please make your request here.
DOWNTIME Series
- Over-Production Don’t get overwhelmed with OVER-PRODUCTION waste
- Non-Utilized Talent NON-UTILIZED TALENT is a costly waste of your most valuable assets
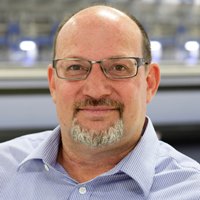