Don’t get overwhelmed with OVER-PRODUCTION waste
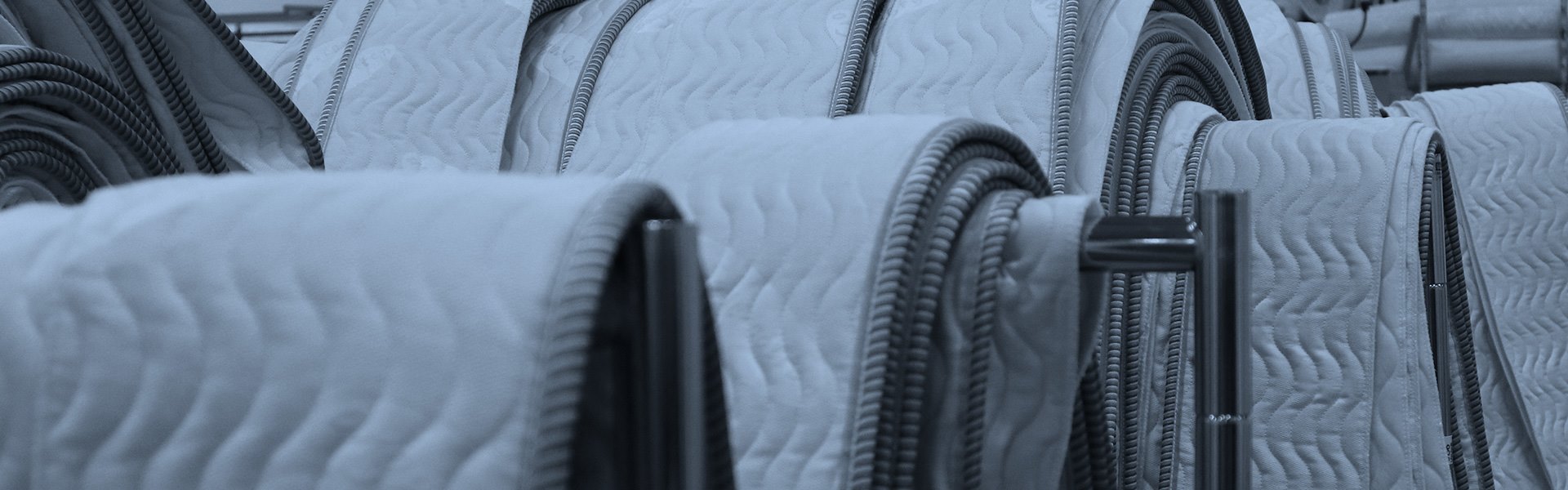
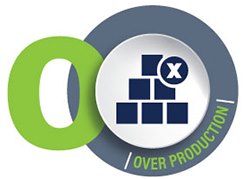
OVER-PRODUCTION waste, one area of waste addressed in lean manufacturing’s “DOWNTIME waste” philosophy, occurs when excessive product is created. “Stocking up” may seem like a good thing, but the truth is, this results in inventory imbalances, costly unnecessary material handling work, and a waste of storage space. Furthermore, if orders never match the finished goods inventory those materials must be scrapped or sold at discounted values.
Just as lean manufacturing practices strives to eliminate all unnecessary “extra” components in the finished product, optimal lean efficiency eliminates any “extra” finished goods. This over-production consumes time and resources that could be utilized in better value-building functions.
- Causes: Poor demand forecasting, miscommunication within the production workflow, and inadequate material handling controls can result in excessive WIP.
- Solutions: Maintain a strict production schedule more closely aligned with real-time needs instead of stockpiling beyond current need.
GSG Solutions
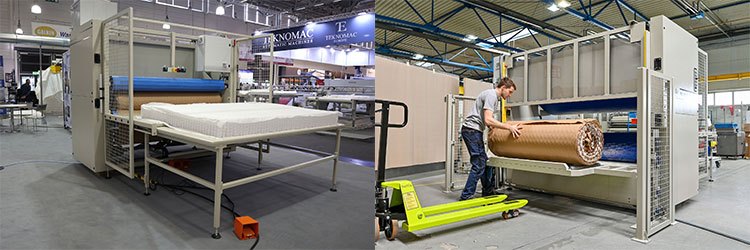
ROA-400RS roll-pack opener is conducive with JIT pull-production styles. Manufacturers may prefer to err on the over-abundance side rather than be at risk of being short of materials during production runs, but the most cost-effective operations only produce to specific needs.
Many mattress producers using roll-packed goods open the entire bale and then stack and sort all the opened goods in a large storage area. The ROA-400RS can dispense units one at a time and even reseal the reminder until they are required. It can operate in a stand-alone fashion or be positioned to insert materials directly into the production line one unit at time.
The Spectrum® is a unique mattress quilter that automatically turns sewing needles on and off, as needed, to form various patterns. Since manual needle setting changes do not have to be performed, there is no need to make long production runs of the same styles. Different products can be made based on real-time needs and maintain a consistent value-add workflow.
Traditional multi-needle quilt machines consist of hundreds of needle settings that often require manually relocating an array of needles within the needle bar arrangements to create different panel designs. Depending on the settings, this can result in hours of non-productive downtime. To make better use of their time, quilting operators often create “panel farms,” excessive piles of finished panels, and then make needle settings at a more convenient time before producing the panels requiring a different needle setting. Obviously, this is highly inefficient.
The high-speed Spectrum eliminates this waste of labor costs and production idleness because it has 15 independent sewing heads. The computerized operating system automatically engages/disengages required sewing heads to produce the desired quilt patterns.

DOWNTIME is a common acronym for eight costly types of waste identified in lean manufacturing methodologies. Some forms of waste are obvious, and easily remedied, but others persist and compound their damage daily.
Defects | Over-Processing | Waiting | Non-Utilized Talent
Transportation | Inventory | Motion | Excess Processing
Read our previous article to learn how damaging DEFECTS waste can be and all other forms of DOWNTIME waste will be examined in upcoming posts.
There are many more examples of GSG equipment that reduce DEFECTS waste in your factory, so connect with your experienced GSG representative to learn about more.
Don’t hesitate to eliminate WAITING waste. We’ll discussed how important it is to level up productivity rates across all processes in our next article.
If you would like to have a FREE DOWNTIME poster from GSG to post in your facilities, please make your request here.
DOWNTIME Series
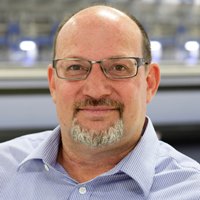