Advantages of the XT9 Glue-less Lamination Process
By Randy Metcalf
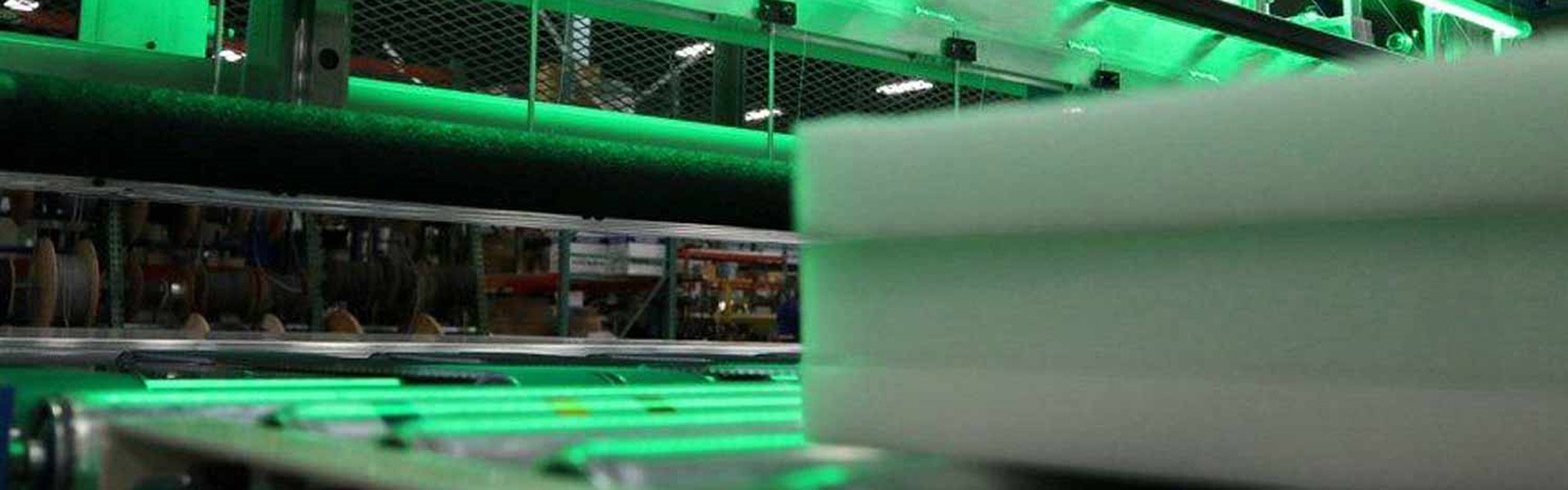
During this time of rising costs, labor shortages, and supply chain disruptions, production efficiencies make the clearest path to more profitable mattress business. Inflation and economic concerns are pressuring consumers to put off large purchases such as mattresses, so producers are reluctant to pass their increasing costs on to the customer. If you don’t raise prices, and already lack surplus labor to cut, the best thing you can do to improve margin is examine processes to maximize value.
The XT9 glue-less lamination process from GSG is a process improvement that checks all the boxes. It enhances the final product and improves the entire process. Manufacturers have joined layers of comfort foam on top of mattresses for years with chemical-based adhesives. It’s an admittedly messy process, but bedding producers have endured the inefficiencies for years with no other available option. Today, there is a new, thread-based option – and it’s better in nearly every way. To prove it, we’ll compare the XT9 to the standard glue process.
How is the standard glue process done?
There are a variety of ways manufacturers have joined these layers, but the most common method is stacking three foam layers using a water-based adhesive roll-coater. Here is an outline of equipment and production details:
- Glue bridge – The glue bridge uses a glue-covered metal roller to distribute adhesive across the surface of the incoming foam sheet. Though each factory may have different costs, an average estimate is about $2.50 per glue layer.
- Dryer – After exiting the glue bridge, the glue-covered foam sheet goes through a super-heated dryer machine to expedite drying of excess moisture. Without this step, the finished layered unit would have to sit approximately 24 hours for a full cure time.
- Repeat next layer – Following this drying process, it reverses back through both machines to add the next foam sheet on top of the first. Both units are then sent through the roll-coater and drying machines to adhere the second layer to the first.
- Add third layer – The final foam sheet can be added on top of the other after the second drying process.
- Mattress press – The glued unit of three foam layers enters a mattress press to compress all three parts. This step helps secure the bond of all glued components.
The total material cost of the glue in this three-layer lamination process is about $5 and the process takes about 145 seconds.
How is the glue-less XT9 lamination process done?
- Build-up – All three foam layers are stacked on top of one another prior to entering the XT9 Stitch Bridge.
- XT9 Stitch Bridge – The layered unit enters the Stitch Bridge, and all layers are joined in a single, 35-second cycle time.
The total cost of thread used in the process is about $0.10 and the cycle time is at least 60% shorter than the glue process.
The XT9 lamination process cuts material costs by over 95% and reduces production steps by 60% and cycle time by approximately 75%. Those are dramatic process improvements, but that doesn’t even factor in additional efficiency concerns.
- The glue system may require extra daily cleaning time. That is an additional, non-value-add labor cost. It cuts into real production time, lowering that treasured per-piece value due to the lowered productivity rate.
- The thread used in the XT9 process has an indefinite shelf life, while most glues have a relatively short one. You are at risk of wasting costly resources if the adhesive is not used within the specified timeframe.
- If layers are accidently glued and dried together in the wrong composition, the expensive foam layers must be scrapped. If the layers are accidently sewn together in the same manner, they can be separated and reused.
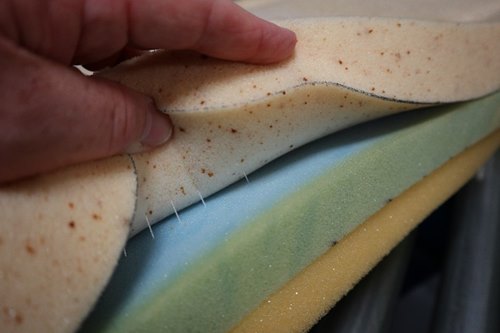
There are pros and cons to every glue lamination process, but the short cycle time and simplified, low-cost process of the XT9 system is more advantageous in nearly every case. There is no room for sloppy inefficiencies in today’s challenging market conditions. The XT9 thread-based lamination method is a leaner way to gain value for every unit you produce.
In this article, we have outlined the reasons the Gribetz XT9 is a logical choice for a lamination process that improves production value. The next post in this two-part series will address some compelling intangible benefits that make your XT9 mattress a bedding market standout.
* All production and cost values are based on average observed estimates; however, all facilities are subject to different conditions and actual results will vary.