A Practical Guide to Automation in the Mattress Factory
By Randy Metcalf
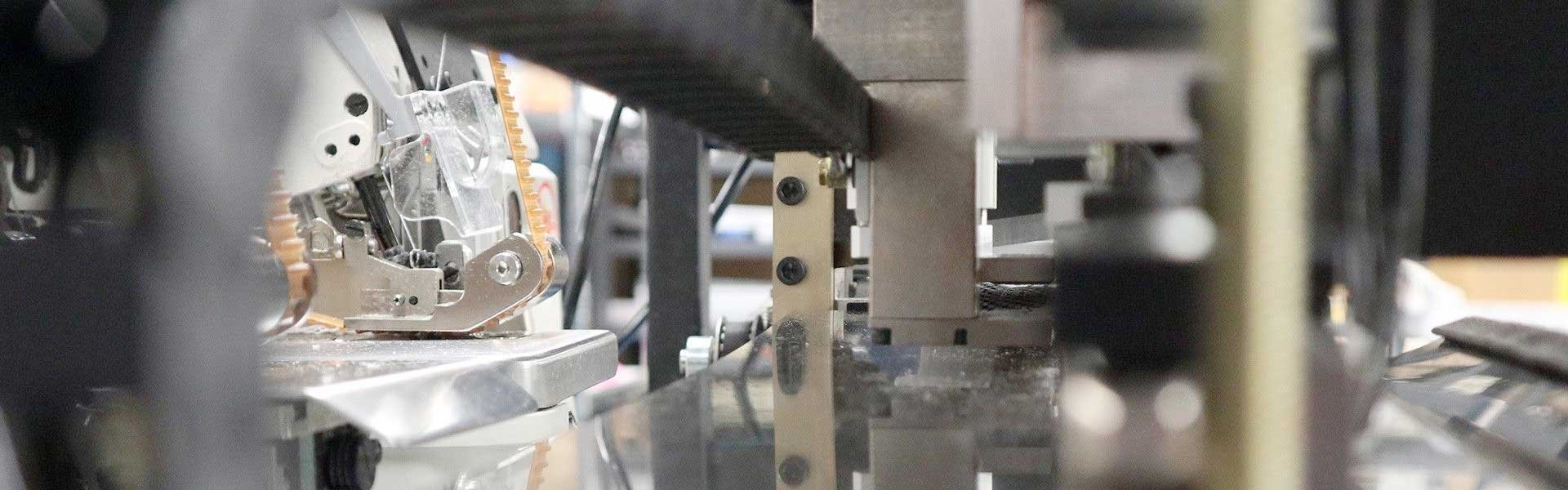
The word “automation” is a broad term that conjures up a different image for different people. Thanks to futuristic tales of science fiction 50 years ago, many still think it means the total conquest of the manufacturing factory by full-scale robots. In truth, there are many degrees of automation and most are much more attainable than you imagine.
In the purest form of the word, automation does imply using mechanical means to replace or reduce your reliance on human activity to perform a task. Your “automatic” garage door opener is a popular example of automation, and that’s not so intimidating, is it?
Let’s look at the manual steps this simple automation has replaced:
- Temporarily park the car
- Get out (possibly in the rain) and walk to the garage door
- Raise the garage door
- Return to the parked car
- Drive the car into the garage
- Get out the car and return to the garage door
- Pull the door closed
Like your garage door opening activity, you need to identify repetitive human activity in your factory and see what can be replaced with automation. Be sure to analyze the sub-tasks involved with the process to make sure nothing is taken for granted. Notice that in the garage door example, only steps three and five add any value to the process. The other five steps are non-value-add activities that offer no benefit to the outcome.
The first step is de-skilling.
If it’s not possible to replace the labor with full automation, simply making the task easier and safer for the employee is a beneficial step. This usually involves a machine specifically designed to execute part of the operation formerly done by the operator – or helps perform the job with less physical effort by the operator. A Mattress Master tape edge machine, which moves the bed for the operator, is a good de-skilling example. Easing the employee’s workload can speed up piecework and enable them to maintain a higher productivity rate for the duration of the workday.
De-skilling the job also helps in the future when it’s necessary to replace staff. You can hire a less-skilled employee at a lower hourly rate, and it will take less time to train them in this de-skilled process. You can also more easily cross-train other workers to perform multiple tasks in de-skilled operations.
Multi-tasking equipment improves productivity exponentially
Machinery makers like GSG have already identified many ways to combine process steps so fewer machines can perform all the tasks required to create the product. Typically, these computer-controlled systems also produce a more consistent final product and piece rate because they remove the element of human error and “personal fatigue and delay” (PF&D) associated with manual operations.
This type of machinery typically performs repetitive tasks that are easily computer-driven like measuring, cutting to size, electronic sensor-controlled sewing, and much more. Most can store hundreds of programmed dimensions in the computer’s storage for batch processing. A BC-200M border machine is a great example of multi-tasking equipment.
As a result, many multi-machine operations with multiple operators can be combined into fewer machines with fewer operators.
Material handling and conveyors
Removing non-value-add touches is critical to improving productivity. If your employees are handling work-in-process (WIP) without adding value to it, that is a waste of money and robs you of profit margin on every single item touched. The most common way this occurs is moving goods from one location to another.
Motorized conveyors, lifting devices, pick-and-place units, and sorting systems can all be integrated into your workflow to reduce manual handling of WIP. This improves your productivity by keeping your labor focused on producing goods, not pushing carts.
A unique solution in this department is Waste-exit. It is a vacuum-powered system, custom-fit to machines, that automatically recognizes material scrap and trimmings falling into hoppers. It then sucks this scrap through ductwork across the plant to a centralized collection point. Sewing machine operators no longer waste their time cleaning their workspace. They are working in a safer environment and improving their productivity.
Robots are available for the mattress factory
As we’ve discovered, automation is not exclusively robotics, and it should be understood there are many nuances within the category of “robot.” Few resemble the walking mechanical androids of science fiction fame. Most are little more than pick-and-place devices that transport units from one spot to another.
Some are equipped with sensors to execute logic-based functions to change the path or handling sequence based on certain criteria, but most simply perform the same repetitive cycle thousands of times over the life of the robotic device. One example of logic-based processes may be the robot analyzing the size of each unit and sorting variously sized units into appropriate different locations.
Some robots have articulated joints and 360-degree motion capabilities to perform more difficult and precise movements. They can be equipped with different gripping mechanisms best suited for the task. Like most emerging technologies, as the computing capacity matures and functional capabilities expand, the ability to perform more complex operations have increased while relative costs have decreased. Factory robotics are a more realistic option than ever before.
Automation – you need it now more than ever
Mattress factory automation has had a foothold in the industry for decades, but in light of today’s labor concerns, changing sales channels, and shrinking profit margins, it has become more valuable than ever. Don’t be intimidated by a misunderstood concept of “automation,” but instead be encouraged by the expanding options available to make your factory more productive – and more profitable.